![]() |
Turbo Project Parts
Updated 10/9/09
Part Needed |
Expected
|
Source |
Obtained? |
Paid |
Turbo - Garret T03, .60 comp A/R, .63 turbine A/R | $175 |
Used - Private Party |
Yes |
$165 |
Turbo - Garret T03, .60 comp A/R, .63 turbine A/R | $175 |
Used - Private Party |
Yes |
$175 |
K&N Air Filter #RE-0910 | $40 each |
Jeg's |
Yes |
$80 |
Header Material | $60 |
Home Depot/McMaster |
Yes |
$200 |
Intercooler | $100-$300 |
Ford Dealer |
Yes |
$230 |
Intake and Exhaust Piping | $50 |
Used/New - Private Party/JCWhitney/local supplier |
Yes |
$150 |
Holley 650 Double-Pumper Carb | $350 |
New - Jeg's |
Yes |
$350 |
Bonnet | $50 |
Fabricated |
Yes |
$10 |
Oil Lines (to turbos) | $80 |
Auto Parts Store |
Yes |
$15 |
Fuel Lines | $50 |
NAPA |
Yes |
$15 |
Exhaust Temp Monitor | $120 |
Jeg's |
Yes |
$115 |
Boost Retard Device - MSD 6BTM | $330 |
Jeg's |
Yes |
$330 |
Blowoff Valve | $45 |
Private Party |
Yes |
$0 |
Connecting Hoses | $30 |
NAPA |
Yes |
$100 |
Miscellaneous (hardware, fittings, etc.) | $50 |
Various |
Yes |
$150 |
What's the source for the turbos? They can be purchased new of course, but I'm too cheap and broke for that. These turbos came on manual-transmission T-Bird Turbos in the mid-'80s so there are lots of them around. The automatic T-Bird Turbos had the same turbo but usually came with a .48 turbine A/R. That basically means it'll spool up faster than the .63, but it'll run out of breath (and become an exhaust restriction) sooner.
Where to get one? eBay comes to mind of course, but I was nervous about buying an expensive
and complex part from some totally unknown party. Junkyards are great, but there aren't too many around
my home town anymore. Besides, I didn't really know what I was looking for in a good turbo. Then I found the jyturbo e-mail list from Yahoo! Groups. I joined up in early December, 2001 and learned a ton of stuff and "met" quite few people as well. I became friends with one guy in particular and he happened to have a nice T3 on hand. Sold! $185 later it was on my kitchen table (wife rolls eyes). A few weeks later I found another one from a different person on that e-mail list for $125. Not as nice, but should work for a couple years without a rebuild.
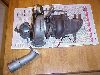
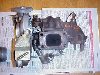
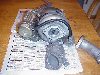
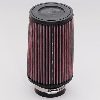
I decided to fabricate them. Fun project, but what should I use? Ever hear of "weld els"? I hadn't, but they are basically your typical schedule 40 "black pipe" you can get at Home Depot for plumbing, but they're cast into a smooth, 90-degree bend with beveled ends for easy butt welding. Except for the weight, they're perfect. The 1.5" weld els have an inside diameter of 1.61" (no, it doesn't make sense to me, either) and an O.D. of 1.90". Right on for my needs. Each 1.5" el costs about $4-$5 so the headers aren't cheap, but I figured the durability and ease of welding would justify the cost. Besides, what option is cheaper? Fabbing your own out of a header kit or buy buying 16-gauge mandrel-bent steel is expensive as well.
I did think about using some 16-gauge, mandrel-bent exhaust tubing, but I was warned that the thin-wall tubing might not stand up to the added heat and weight of the turbo hanging from it, so I went with the schedule 40 stuff. The straight tubing is from Home Depot, about $2/foot (2002 prices). The weld els I had to buy from an industrial plumbing supply place. You can also get them online at www.mcmaster.com.
Here's what the weld els look like. There is one 2.5" el and two 1.5" els:
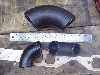
Here's the passenger's side header in various stages of construction. I had to make the ends that
mate to the flange into an oval shape because the header bolts are right next to the ports. Add in
the thick-wall tubing and there's not much room left over!
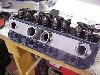
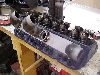
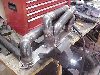
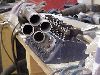
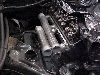
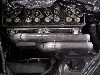
Here it is with the collector fabbed up and welded on, then with the turbo mounted, and finally
after adding the driver's side header:
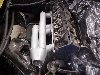
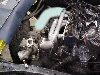
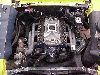
And some shots before coating the pipes:
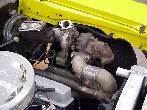
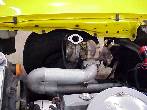
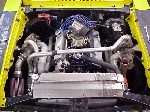
If I were to do it over, I'd strongly consider trying to find some 14-gauge mild steel tubing for the headers. The weld els are very strong and easy to weld due to their wall thickness, but they are just so freakin' heavy. I haven't weighed them in their final configuration, but I really should. I think that before I did the funky 180-degree bend at the ends they weighed 30 pounds each, so together they probably weigh 75 pounds now, right over the front end where you don't want any additional weight! Ahh, if only I didn't have $150 and countless hours into the headers already...
I bought an ATI ProCharger intercooler from a friend of a friend to run on my Nova, but it just wouldn't fit
very well at all. The core itself was 27" x 6", and the overall size was about 31" x 11". Too wide, and too
short to be a good fit. The only place it could go was where the radiator normally is and it would leave big
gaps around it...it just wasn't a good match.
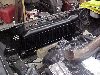
Next, I bought an intercooler intended for a 2001 Ford SuperDuty truck with a Powerstroke diesel engine. Here it is sitting where my radiator normally goes. Much, much better fit than the ATI! I did have to notch the frame and do some cutting on the core support, but I'm glad I went this route. It sure wasn't the first time I cut up my car.
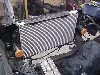

I used 1.5" pipe from the compressor outlets to a point near the intercooler and merged them into a 3" pipe. I've since learned that may be restrictive and will upsize it, probably to 2". As for the downpipes, I bought some 2.5" stock replacement flange sections from the parts store to match up to the turbo outlet flange and Mickey-Mouse'd some pipe between those and the existing 3" pipes under the car. The passenger's side was easy and direct, the driver's side was another story. See the Turbo Progress page for more info. I'll have to rework that setup at some point.
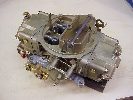
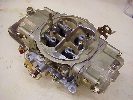
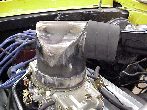
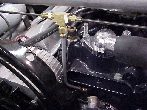
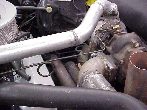
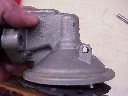
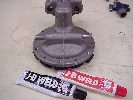
I went mainstream on this and just bought an Autometer UltraLite pyrometer with thermocouple and probe for $115. It's much cheaper (although much less informative) than a wideband oxygen sensor system.
Enter MSD with their 6BTM ignition box. It's basically a 6AL box with their Boost Timing Master built in. The BTM will allow me (via a cockpit-adjustable control) to retard the timing anywhere from one to three degrees per pound of boost up to 15 degrees total retard. Perfect! That way I can run about 15 initial plus 20 centrifugal, but under full boost I'll be back at 20 total, which is a common advance amount for turbo cars. I'll play with the timing to see what's best while staying out of detonation. I like the added margin of safety this controller should give. Besides, I'll have the multiple-spark discharge and a built-in rev limiter. I'm already impressed by how much the MSD box has smoothed out my idle! The engine starts and idles much better than it did before I added the box. I love it.
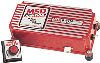
Copyright © 2009 Bruce Johnson and Craig Watson